Top Metal Stamping Solutions for High-Quality and Cost-Effective Manufacturing
Advanced Techniques in Steel Stamping for Precision Production
As sectors constantly require better tolerances and elaborate layouts in their steel components, the mission for innovative techniques in metal marking has actually magnified. From the application of sophisticated multi-stage stamping processes to the combination of advanced automation modern technologies, the landscape of steel stamping is undergoing a profound improvement.
Advanced Multi-Stage Stamping Procedures
Reviewing the intricacies of sophisticated multi-stage stamping processes exposes the innovative strategies used in modern manufacturing practices. Metal Stamping. Multi-stage stamping is a complex process that includes several steps to transform a flat sheet of metal into a final stamped product. The usage of dynamic passes away, where various procedures are done at each phase of the marking procedure, permits for high accuracy and performance in the production of detailed steel components
Throughout the initial stages of multi-stage marking, the level steel sheet is fed into the stamping press, where a series of dies are made use of to reduce and form the material. Subsequent stages entail added developing, bending, and punching operations to further improve the component. Each stage is carefully developed to develop upon the previous one, leading to the production of complicated geometries with tight tolerances.
Advanced multi-stage marking processes require a high level of knowledge and precision to ensure the top quality and uniformity of the stamped parts. By making use of innovative machinery and tooling, manufacturers can generate a large variety of metal parts with effectiveness and accuracy.
Accuracy Tooling Innovations
Precision tooling innovations have actually reinvented the metal marking industry, boosting effectiveness and quality in making processes. These innovations have significantly influenced the way steel elements are produced, causing higher accuracy and consistency in the final products. One crucial innovation is the growth of computer mathematical control (CNC) technology in tooling layout and construction. CNC systems enable intricate designs to be converted straight into tooling, guaranteeing accuracy and repeatability in the marking procedure.
In addition, the integration of sensors and real-time monitoring abilities in precision tooling has allowed makers to identify and resolve concerns promptly, minimizing downtime and decreasing scrap rates. By incorporating clever modern technology into tooling, drivers can maximize parameters such as pressure, rate, and alignment throughout the stamping operation, leading to boosted item high quality and enhanced efficiency.
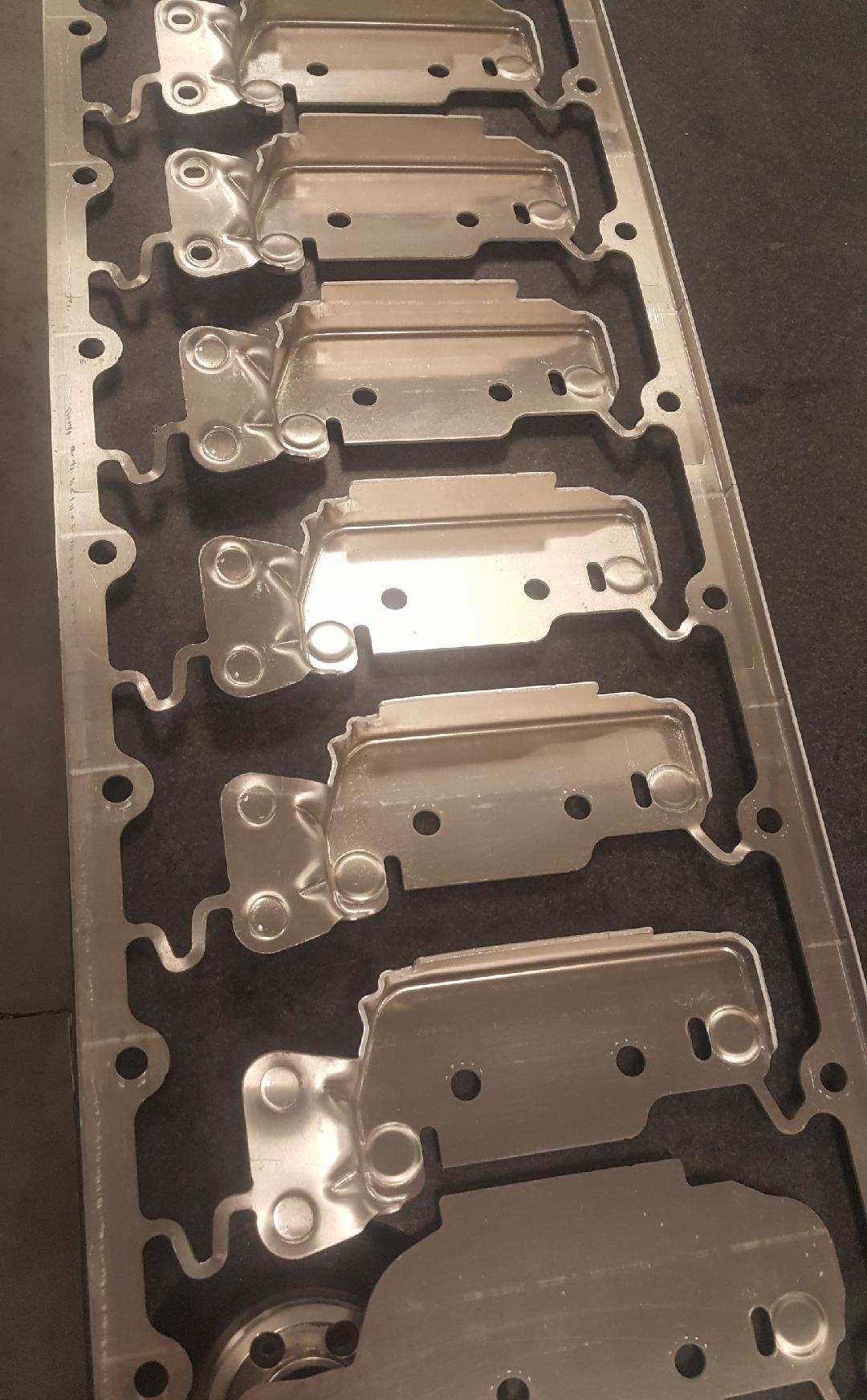
Automation in Steel Stamping
The development of precision tooling developments in the metal stamping sector has actually led the way for considerable developments in automation, transforming the production landscape in the direction of boosted effectiveness and productivity. Metal Stamping. Automation in steel marking includes using innovative equipment and robotics to carry out various jobs commonly performed by human operators. This shift in click this link the direction of automation uses various benefits, consisting of enhanced accuracy, much faster production cycles, and reduced labor prices
One secret aspect of automation in steel stamping is the execution of computer system numerical control (CNC) systems, which make it possible for exact control over the stamping procedure. CNC innovation permits the production of complicated and elaborate steel get rid of constant top quality. Furthermore, automated systems can be programmed to run continuously, bring about higher output prices and shorter preparations.
Additionally, automation enhances work environment safety by lowering hand-operated handling of heavy products and reducing the risk of accidents (Metal Stamping). As making industries remain to welcome automation, the future of metal stamping holds great pledge for also greater effectiveness and technology
High-Speed Stamping Techniques
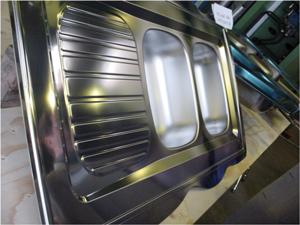
One of the primary advantages of high-speed stamping techniques is the capability to create a big volume of parts in a shorter amount of time compared to standard stamping techniques. This boosted efficiency not just enables makers to satisfy limited production due dates however likewise enables cost savings through economies of scale. Additionally, her latest blog high-speed stamping can help in reducing product waste by maximizing the product use Visit Website throughout the stamping process.
Additionally, high-speed stamping techniques frequently incorporate innovative features such as fast die adjustment systems and real-time tracking capabilities, even more enhancing the total performance and adaptability of the steel stamping procedure. As modern technology proceeds to advancement, high-speed stamping is anticipated to play a vital function in driving the future of accuracy production.
High Quality Control in Stamping Operations
Reliable quality assurance steps are essential for making certain the dependability and consistency of steel stamping procedures. Quality control in marking operations involves a collection of systematic procedures targeted at finding and avoiding flaws in the produced components. One vital facet of quality control in steel marking is making use of innovative assessment techniques such as optical assessment systems and coordinate measuring makers (CMMs) to validate the measurements and tolerances of stamped parts.
In addition, quality assurance actions in stamping procedures often include the execution of statistical process control (copyright) approaches to monitor the manufacturing procedure in real-time and ensure that it stays within appropriate limits. By evaluating information and recognizing trends, makers can proactively resolve any discrepancies from the wanted top quality standards.
Additionally, high quality control in steel marking procedures additionally involves detailed product screening to ensure that the raw materials utilized satisfy the called for requirements for the stamping process. This may include conducting material firmness examinations, tensile stamina examinations, and dimensional examinations to assure the quality and integrity of the stamped components. In general, executing robust quality assurance procedures is vital for achieving high-quality stamped components consistently.
Conclusion
To conclude, progressed strategies in steel marking play a critical duty in accuracy production processes. Through multi-stage stamping procedures, ingenious tooling options, automation, high-speed methods, and extensive quality assurance measures, makers can accomplish higher degrees of accuracy and performance in their procedures. These developments in metal stamping innovation have enabled firms to generate complicated parts with limited resistances, ultimately leading to boosted item quality and consumer contentment in the production industry.